The New Sustainable Plastic Replacement Hitting the Market

Creating a carbon-negative plastic replacement from sustainably farmed seaweed has myriad benefits – and income streams.
What is it?
“We’ve developed a new material derived from the ocean that has the potential to replace plastic at scale,” says Michael Kingsbury, a former mergers and acquisitions lawyer. “We call it Uluu – it’s made of seaweed, is home-compostable and biodegradable and has very good oxygen and moisturebarrier properties so it can be used in ways other bioplastics can’t because they tend to be water soluble.”
Where did the idea come from?
“For the past decade or so, I’ve been obsessed about finding ways to solve plastic pollution, particularly when it comes to the problems it’s creating in our oceans,” says Dr Julia Reisser, a marine scientist who has worked for Andrew and Nicola Forrest’s Minderoo Foundation. “When I dug into it, I realised that recycling is important but it’s cleaning up the past. To solve the problem, we need to come up with a material that isn’t made of fossil fuels and doesn’t create pollution during its production, use or after we dispose of it.” She began researching using seaweed to make polyhydroxyalkanoates, aka PHAs, a natural polymer. “Seaweed mitigates a lot of problems in the oceans and using farmed seaweed creates sustainable jobs in coastal communities, which helps us tackle overfishing.”
How did you get it off the ground?
Reisser left her job and started looking for a co-founder. “I finally found Michael, who handles the finance, commercial and strategy side – a complementary skill set to mine.” In 2021, they raised $1.8 million of pre-seed funding, got a lab with the University of Western Australia’s support and set about the proof of concept. “We take seaweed and ferment it in saltwater, similar to brewing. Microbes digest the seaweed and turn it into PHAs. Some PHAs are long-chain polymers, some are short, some elastic, some rigid. What’s beautiful about PHAs is they can be as versatile as plastic.”
What have you learnt?
In December last year, with the help of scientists at CSIRO Manufacturing, Uluu produced a set of transparent, flexible films and injection-moulded rigid discs. Reisser says it showed that the material can work with existing polymer-production equipment to ensure a cost-effective transition. It takes about 10 kilograms of seaweed to produce one kilogram of PHAs. The seaweed is milled and omega-rich oils can be extracted from it for an additional revenue stream. The leftover seaweed biomass is protein-rich and could become carbon-neutral fish feed, an environmental and economic win.
What’s next?
Uluu is building a pilot plant in WA and hiring more scientists. “We need lots of engineering and R&D as we scale up,” says Reisser. In June, it won the inaugural KPMG Nature Positive Challenge. “The prize was $100,000 but we’re even more excited about the pro-bono advisory support. They’ll help us research sourcing seaweed because both the economics of our business and the social and environmental returns are closely correlated to how we do that.” Initially, Indonesia, where many seaweed farmers are women, will be the main source. And they’re working with brands to supply “Made with Uluu” products by late 2023.
Need to know
Founders: Michael Kingsbury, 33, and Dr Julia Reisser, 38
First customer: An undisclosed outdoors brand, with products made from Uluu expected to be on sale in 2023
Investors: Main Sequence, Alberts, Possible Ventures, Startmate and more
Headquarters: Perth
Employees: 13
Market valuation: Not disclosed
SEE ALSO: Bringing Medical Innovation Back To Australia with Neo-Bionica
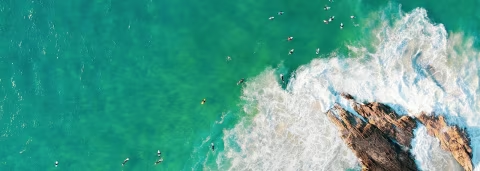